Designed to remove chips and waste from cutting zone. Chips fall into a special chamber mounted on the spindle and are removed through a special pipe into the dust collector.

VOLTER SX series CNC Routers have processing area 1 020 * 1 200 mm. This is the ideal solution for the production of small parts.
Larger ball screws with a higher pitch and more powerful servo motors, increased feed rate (200mm/s) and thus significantly increased the desired productivity of the machine.
This model has been fitted with a more robust gantry tube to increase production tolerances, which also allows us to fit more powerful spindles and the ability to milling materials up to 350mm in thickness.
Controller | VOLTER CS |
Processing area, mm. | 1 020 * 1 200 |
Type and quantity of motors | 4 servo motors 750W |
Max travel speed on X and Y axes, mm./sec. | 250 |
Max travel speed on Z axis mm./sec. | 100 |
Max thickness of material , mm. | 350 |
Spindle power, kW | 4.5 to 6.6 |
Spindle rotation speed, RPM | from 1 000 to 24 000 |
Tool clamping | Mechanical or pneumatic |
Type of drives for X and Y axes | Servo, ball screw |
Type of drive for Z axis | Servo, ball screw |
Control panel | 10" touch monitor |
Model | Processing area, mm | Dimensions, mm | Weight, kg |
---|---|---|---|
VOLTER SX | 1 020 * 1 200 mm | 2 140 * 1 770 * 1 940 mm | 600 |
Options
Steel frames of VOLTER machines is welded from cold-rolled steel pipes. Each frame undergoes thermal stabilization to maintain its geometric dimensions for the full lifetime of the machine. The seats for the installation of linear guides and helical racks are processed by high-precision machining center.
Touch-screen monitor is the main control panel of VOLTER CNC Routers. This monitor allows to control processing and change settings. User friendly interface has a modern, convenient and intuitive design.
VOLTER CNC Routers have air-cooled spindles from HITECO (Italy) company with power from 4.5 to 10 kW. ER32 collets are used for all spindles. There is a choice between spindles with pneumatic or mechanical clamping. The maximum rotation speed is 24 000 RPM.
Vacuum hold down is the most effitient solution for fixing the material on the machine during processing. The vacuum table consists of extruded aluminum profiles, a sacrificial PVC layer and a system of hvacuum valves for controlling the vacuum zones. Quantity of vacuum zones varies from 4 to 12 depending on the size of the working field of the machine.

The sensor allows to measure the length of the bit quickly and accurately. It is enough to push a botton on touch screen monitor. Results of this measurement will be saved in the controller, which prevents damage of the working surface of the machine.
Laser pointer allows operator to set starting point of a job quickly and easily. It is enough for it to move the laser pointer to angle of sheet and click "Save" button on the touch screen monitor.
VECTRIC VCarve Pro software to create and prepare 2D and 3D files for CNC Routers. Large selection of formats for importing files, intuitive interface.
This system automatically changes tools during processing. It lets to save time for jobs which need several tools for processing. Controller saves length of each tool in the system. As result, it is not nesesarry to measure tool length after changing of a tool by this system. VOLTER automatic tool changer has 7 positions for tools.
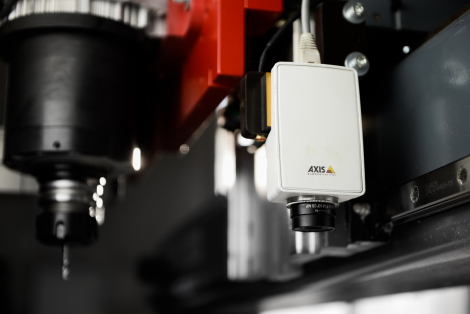
The option allows to cut the printed image along the contour. When preparing a file for printing, marks are added to the file — black circles with a diameter of 5-8 mm placed behind the contour of the image to be cut.
Printed image is placed on the machine and after starting the job, the camera checks locations of marks. Special software of the machine make adjustments to the job file. It lets to cut printed image exactly on the contour regardless of geometric distortions encountered in print and location of printed image on the machine.

The system carries out a dosed supply to the cutting zone of lubricant emulsion or air flow. Continuous supply of lubricant (in the form of oil mist) or compressed air lets to maximize tool lifetime, improve quality of processing and increase speed of processing. It is necessary to connect an external pressed air supply with a working pressure of at least 6 bar to operate this lubrication system.

This knife is efficient and reliable solution for cutting polymer materials and corrugated board. The main application is cutting along the contour of figures from corrugated cardboard, sheet vinyl, and other polymer sheets. The principle of operation of this knife is that the cutter has free rotation. Tip of the blade due has displacement relative to the axis of rotation. As result, the knife is turned by the cutting edge in the direction of tool movement due to the material resistance.
High efficient 7.5 kW vortex blower is supplied complete with air filter, pressure gauge, safety valve and fittings for connecting to the machine. Do not require maintenance during the entire life cycle.
Rotary vacuum pumps Busch MINK (Germany) are an effective and reliable solution for vacuum hold down of materials. The cam rotors do not come into contact with each other or with the cylinder in which they rotate. The extremely small clearances between the cam rotors and the casing optimize the internal seal and guarantee a consistently high pumping speed without using of lubricating fluids.
TS 220 is a reliable industrial dust collector for removing chips and dust during processing of various materials. The model is designed to work in the most hard operating conditions. Equipped with an industrial three-phase electric motor 400 V / 2200 W and a vacuum turbine with a side channel. The dust collector has a 30 l chip storage tank.
TS 300 is a reliable industrial dust collector for removing chips and dust during processing of various materials. The model is designed to work in the most hard operating conditions. Equipped with an industrial three-phase electric motor 400 V / 2200 W and a vacuum turbine with a side channel. The dust collector has a 100 l chip storage tank.